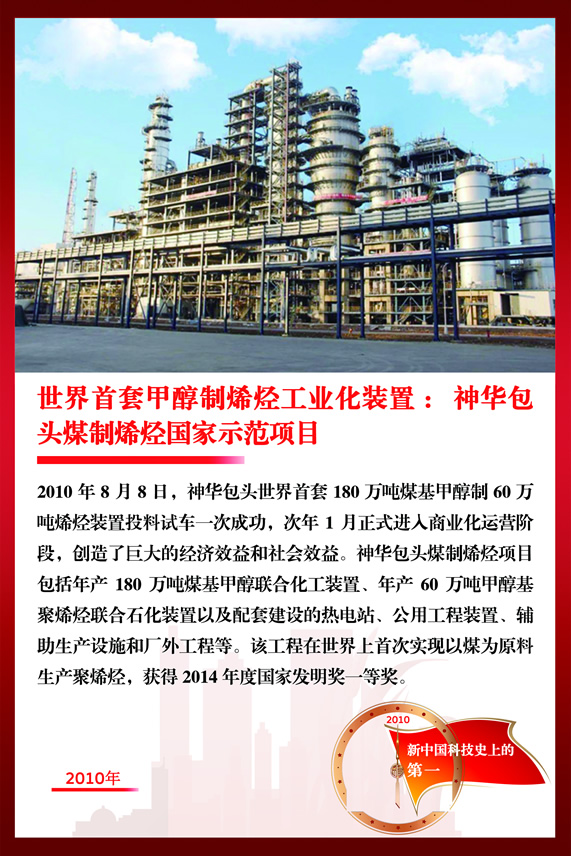
成果簡介 2010年8月8日,神華包頭世界首套180萬噸煤基甲醇制60萬噸烯烴裝置投料試車一次成功,次年1月正式進入商業(yè)化運營階段,創(chuàng)造了巨大的經(jīng)濟效益和社會效益。神華包頭煤制烯烴項目包括年產(chǎn)180萬噸煤基甲醇聯(lián)合化工裝置、年產(chǎn)60萬噸甲醇基聚烯烴聯(lián)合石化裝置以及配套建設(shè)的熱電站、公用工程裝置、輔助生產(chǎn)設(shè)施和廠外工程等。該工程是世界首套以煤為原料生產(chǎn)聚烯烴的項目,獲得2014年度國家發(fā)明獎一等獎。 歷史背景 乙烯、丙烯等低碳烯烴是重要的基本有機化工原料,是現(xiàn)代化學工業(yè)的基石,其傳統(tǒng)生產(chǎn)技術(shù)強烈地依賴石油資源。由于我國石油資源不足,這些行業(yè)的發(fā)展受到嚴重制約。但我國煤炭資源相對豐富,發(fā)展以煤為原料制取石油類產(chǎn)品的煤化工技術(shù),是關(guān)系到我國經(jīng)濟長期穩(wěn)定發(fā)展和能源安全的重大課題。其中,煤制烯烴技術(shù)是最重要的發(fā)展方向,其關(guān)鍵核心技術(shù)是甲醇制烯烴技術(shù)。多年來,針對我國石油產(chǎn)量不足、進口需求量逐年增加的情況,中央提出加快實施以甲醇、乙醇、二甲醚、煤制油等作為石油替代品的計劃。在這種背景下,以甲醇為原料生產(chǎn)低碳烯烴的MTO技術(shù),成為發(fā)展新型煤化工產(chǎn)業(yè)、實現(xiàn)國家“以煤代油”戰(zhàn)略的必由之路。 創(chuàng)新歷程 國家有關(guān)部委和中科院立足國情,早在“六五”期間就把非石油路線制取低碳烯烴列為重大項目,并給予重點和連續(xù)支持。中科院大連化學物理研究所根據(jù)國家發(fā)展需要,從20世紀80年代初便開始了用天然氣或煤制取低碳烯烴的研究工作,先后完成了催化劑制備、放大及固定床和流化床兩次中試,在催化劑和反應(yīng)工藝等核心技術(shù)方面不斷取得突破。20世紀90年代中期,中科院大連化學物理研究所、美國UOP公司先后完成MTO中試。由于當時原油價格相對偏低、甲醇的大型化生產(chǎn)技術(shù)還不成熟等原因,該技術(shù)在國內(nèi)外都未實現(xiàn)工業(yè)化應(yīng)用。
2004年8月,中科院大連化學物理研究所提供具有自主知識產(chǎn)權(quán)的催化劑和循環(huán)流化床中試技術(shù)成果,陜西新興煤化工科技發(fā)展有限責任公司出資進行裝置建設(shè)及管理,中國石化集團洛陽石油化工工程公司進行工程設(shè)計,三家發(fā)揮各自優(yōu)勢開展合作,共同進行日處理甲醇50噸的工業(yè)化試驗。經(jīng)過兩年的通力合作,“甲醇制取低碳烯烴(DMTO)技術(shù)開發(fā)”工業(yè)性試驗項目取得重大突破性進展,在日處理甲醇50噸的工業(yè)化試驗裝置上實現(xiàn)了甲醇轉(zhuǎn)化率接近100%、低碳烯烴(乙烯、丙烯、丁烯)選擇性達90%以上的目標。
2006年8月23日,世界首套萬噸級甲醇制低碳烯烴(DMTO)裝置工業(yè)試驗項目通過了國家級鑒定。該項目在甲醇處理量為50噸/天時,甲醇轉(zhuǎn)化率接近100%,低碳烯烴(乙烯、丙烯、丁烯)選擇性達90%以上。大連化物所首次將SAPO-34催化材料應(yīng)用于甲醇制烯烴的催化過程,開發(fā)了相應(yīng)的催化劑和與之配套的循環(huán)流化床中試技術(shù),并利用該中試技術(shù)建成了目前世界上第一套萬噸級甲醇制烯烴工業(yè)化裝置。該項技術(shù)具有自主知識產(chǎn)權(quán),相關(guān)指標處于國際領(lǐng)先水平。試驗裝置成功運轉(zhuǎn)后,中科院大連化學物理研究所又繼續(xù)開展了大型化DMTO工業(yè)裝置的建設(shè)。
2006年12月11日,國家發(fā)展與改革委員會核準了神華包頭煤制烯烴項目,這是“十一五”期間國家核準的唯一一個特大型煤制烯烴工業(yè)化示范項目,是世界首套、全球最大的,以煤為原料,通過煤氣化制甲醇、甲醇轉(zhuǎn)化制烯烴、烯烴聚合生產(chǎn)聚烯烴的特大煤化工項目。2009年12月26日,化工裝置(甲醇合成及上游)全部建成并中交,2010年1月16日,熱電裝置全部建成并投入使用,2010年2月6日,公用工程裝置全部建成并中交,2010年5月28日,石化裝置(甲醇制烯烷及下游)全部建成并中交。2010年8月8日甲醇一次投料成功,裝置運行平穩(wěn),甲醇轉(zhuǎn)化率達到99.9%以上,乙烯加丙烯選擇性達到80%以上,所生產(chǎn)的乙烯、丙烯等產(chǎn)品完全符合聚合級烯炷產(chǎn)品的規(guī)格要求。8月10日合格烯燈氣體引入烯炷分離裝置,8月13日烯焼分離裝置生產(chǎn)出合格聚合級丙烯和聚合級乙烯,8月15日和21日聚丙烯和聚乙烯裝置分別生產(chǎn)出合格聚丙烯和聚乙烯顆粒產(chǎn)品,提前40天實現(xiàn)了預(yù)定目標。到2010年9月29日,投料試車期結(jié)束,累計生產(chǎn)3.6萬噸聚烯炷產(chǎn)品。2011年3月23日到3月26日,進行了72小時性能考核,設(shè)備的反應(yīng)壓力、再生壓力、水洗水循環(huán)量、污水汽提塔進料量、反應(yīng)密相藏量、再生密相藏量、甲醇進料量、產(chǎn)品氣流量等指標基本在設(shè)計范圍內(nèi)。 重大意義和深遠影響 神華包頭煤制烯烴項目的建設(shè),開創(chuàng)了我國煤制烯烴大規(guī)模工業(yè)化生產(chǎn)和煤化工新產(chǎn)業(yè)的先河,尤其是項目中采用的具有我國自主知識產(chǎn)權(quán)的DMTO技術(shù),標志著我國在煤制烯烴產(chǎn)業(yè)化道路上又邁出了關(guān)鍵一步,對發(fā)展我國清潔煤化工產(chǎn)業(yè)、奠定中國在煤基烯烴工業(yè)化生產(chǎn)領(lǐng)域的國際領(lǐng)先地位,無疑都具有里程碑式的意義。
|